MINI est une marque de voiture du groupe BMW. Il vous explique que la MINI a été élaborée dès l'origine en vue d'un recyclage optimal. Il veille à utiliser le plus souvent possible des matériaux recyclables, à limiter la diversité des matériaux utilisés et à effectuer des assemblages propices au démontage. Dès les premiers stades de la conception, la marque souligne que les ingénieurs de la MINI font attention à ce qu'aucune pièce ni composant ne contienne de matériaux dangereux. Parallèlement aux processus de recyclage déjà en place pour les composants métalliques, des processus similaires pour les pièces en plastique ont été développés, toujours plus nombreuses à bord d'une automobile. En termes de poids, 10% des pièces en plastique de la MINI sont réalisés en matières recyclées.
Pour garantir un taux de recyclage optimal de la MINI, l'emploi de matériaux propices au recyclage et de techniques de construction facilitant le recyclage est privilégié dès les premières étapes de fabrication. Les ingénieurs d'études en charge du projet s'appuient sur des normes spécialement élaborées à cette fin ainsi que sur un manuel détaillant les principes de construction du véhicule dans la perspective de son recyclage. Des techniques d'assemblage optimisées et une sélection rationnelle des matériaux permettent un désassemblage économique d'un grand nombre de composants de la MINI. La coquille externe du tableau de bord et le panneau monté en dessous de celui-ci forment un ensemble dit "mono-matériau" constitué de ABS-PC. Le revêtement de la plage arrière et les panneaux des sièges sont des exemples d'éléments exclusivement réalisés en plastiques . Le revêtement de la plage arrière est fixé au moyen d'un simple rivet à expansion et se détache en un tour de main. Après desserrage de la vis latérale, le panneau arrière du siège avant peut être désolidarisé de ses fixations à agrafes et rivets. Ces composants sont recyclables à 100%.
De manière générale, l'application rigoureuse de la "philosophie du recyclage dès la conception" lors du développement a fait en sorte que la MINI, dès son entrée en production, respectait déjà les quotas de recyclage stipulés dans la directive UE relative aux véhicules hors d'usage destinés à entrer en vigueur d'ici 2015. MINI vous détaille les étapes du recyclage :
I) LE PROCESSUS DE DEPOLLUTION
Le prétraitement commence avec le déploiement des airbags et des autres dispositifs pyrotechniques. Le véhicule est ensuite conduit au poste de dépollution où a lieu l'essentiel du travail. Pour simplifier les opérations, la MINI est équipée de vis de vidange aisément accessibles ainsi que de points de percement marqués destinés à permettre une vidange rapide et aisée de tous les fluides fonctionnels. La MINI est purgée des fluides réfrigérants et des gaz du système de climatisation. Les liquides de freinage et de refroidissement, les huiles du moteur et de la boîte de vitesses ainsi que les quantités résiduelles de carburant sont vidés à l'aide d'outils d'aspiration de conception spéciale et de forets à sécurité intrinsèque. Les différents liquides sont ensuite filtrés et purifiés en vue d'un éventuel réemploi.
Composants pyrotechniques
Les composants pyrotechniques tels que les airbags et les prétensionneurs de ceinture sont déclenchés à l'aide d'un dispositif de déclenchement normalisé. Cette action les neutralise, éliminant de la sorte les risques qu'ils pourraient représenter dans la suite du processus de recyclage et de désassemblage.
Batterie
Après déconnexion et démontage, la batterie est envoyée à une usine de recyclage spécialisée où elle est entièrement broyée. Les plastiques PP sont extraits et regranulés. Le regranulat est ensuite utilisé pour fabriquer des pièces en plastique PP. Le plomb de la batterie est fondu et reconstitué en blocs que l'on utilise ensuite comme matière première dans l'industrie de traitement du plomb.
Huile
Les huiles de vidange peuvent être raffinées et réutilisées dans la production d'huile neuve.
Essence
Lors du processus de désassemblage, l'essence résiduelle est extraite de la MINI par percement d'un trou au point le plus bas du réservoir. Après aspiration, le trou est rebouché. L'essence résiduelle ainsi récupérée est alors utilisée soit comme combustible soit comme carburant.
Liquide de freinage
Le liquide de freinage vidangé est décontaminé par évaporation à film sous vide afin de réduire sa teneur en eau. Le recyclat peut être réutilisé dans la production de liquide de freinage neuf.
II) LE PROCESSUS DE DESASSEMBLAGE
Le réemploi et la récupération permettent d'accroître le taux de recyclage des véhicules hors d'usage. Pour les parties métalliques, le réemploi et le recyclage s'effectuent selon un processus désormais bien établi. Les métaux ferreux constituent les matériaux prédominants dans un véhicule et à ce titre pèsent le plus lourd dans les éléments recyclés qui sont directement réinjectés dans l'industrie métallurgique. Les pièces et les composants peuvent être désassemblés en vue d'être réemployés pour un usage similaire à celui d'origine. Le verre et un grand nombre de matières plastiques peuvent être récupérés et recyclés soit chez le démolisseur, soit après le processus de broyage.
Moteur
En fonction de son état, le moteur de la MINI sera soit démonté, soit arraché à l'aide d'un manipulateur. Il est ensuite soit vendu directement soit envoyé à l'unité de production des pièces de rechange MINI. Là-bas, il subit un désassemblage et un nettoyage avant que ses pièces usagées ne soient remplacées. Le moteur est ensuite réassemblé et proposé aux clients comme moteur de remplacement. L'ensemble moteur-boîte peut également être revalorisé en tant que déchet riche en métal. La ferraille est alors broyée. Après triage, les métaux récupérés (acier, aluminium et magnésium) sont réemployés en métallurgie.
Convertisseur catalytique
Le convertisseur catalytique de la MINI est démantelé à l'aide de cisailles hydrauliques et les métaux précieux (platine, rhodium, palladium) sont réintroduits dans le cycle de production. Ils servent entre autres à fabriquer de nouveaux convertisseurs catalytiques pour la MINI.
Verre
Durant le processus de désassemblage, le pare-brise de la MINI est déposé à l'aide d'une machine à scier ou à fraiser. Les vitres latérales et la lunette arrière sont démontées par extraction. Les panneaux de verre sont ensuite envoyés à une usine de recyclage de verre à vitre, où ils sont broyés en petits morceaux de la taille d'un petit pois. Ces morceaux sont ensuite triés et débarrassés du verre teinté et d'éventuels corps étrangers au moyen de souffleurs haute pression. Le verre recyclé fait partie intégrante du processus de fabrication du verre, la plus grande partie servant à fabriquer des bouteilles et des bocaux.
Jantes en alliage
Pendant le processus de désassemblage, les roues sont démontées des essieux et les pneus séparés des jantes. Les jantes en alliage sont ensuite fondues et recyclées pour fabriquer de l'aluminium de deuxième fusion.
Garnitures de pare-chocs
Après dépose des pare-chocs les éléments en plastique sont séparés des éléments métalliques. Le démontage rapide des garnitures des pare-chocs en plastique est garanti par les mesures prises au premier stade du développement. Tous les éléments de fixation sont aisément accessibles. La structure des garnitures a été conçue pour favoriser un désassemblage économiquement viable. Les parties en aluminium des garnitures sont triées pour être recyclées. Les matières plastiques sont broyées, débarrassées de leur peinture de finition, puis regranulées. Les recyclats servent à fabriquer toute une série d'éléments tels que les garnitures de passages de roue (en termes de poids, 10% des pièces en plastique de la MINI sont réalisées à partir de recyclats).
Panneaux des sièges arrière
Après démontage, les panneaux du bâti des sièges arrière de la MINI sont broyés et fondus pour donner des regranulats.
Revêtement du tableau de bord
La coquille externe du tableau de bord et le panneau monté en dessous de celui-ci forment un ensemble dit "monomatériau" constitué de ABS-PC. Outre le choix du matériau, ces composants ont également été conçue pour favoriser un recyclage économique grâce à une technique d'assemblage basée sur des vis Torx à desserrage rapide et optimisée à cette fin. Tous les composants en plastique possèdent un étiquetage indiquant leurs matériaux constitutifs, gage d'une identification rapide en vue du triage et dès lors, d'un recyclage de première qualité des matières plastiques utilisées dans la MINI. Le revêtement du tableau de bord est broyé, fondu, filtré puis regranulé.
III) LE PROCESSUS DE BROYAGE
Le plus souvent après compression ou aplatissement préalable, la carcasse du véhicule est conduite au broyeur. Les débris passent à travers toute une série de processus mécaniques et physiques de découpage et de broyage avant d'être triés par matière (plastique, textiles, verre et mousse), par taille et par teneur en métal.
Carrosserie
Le broyeur réduit les carcasses en éléments de la taille de la paume d'une main. Un séparateur à air se charge de trier les pièces légères en plastique, le cuir, les tapis et les textiles que l'on réemploie ensuite pour produire de l'énergie. Les pièces à teneur métallique sont séparées à l'aide d'un électro-aimant. Dans une usine de retraitement spécialisée utilisant des techniques densimétriques, les pièces non métalliques seront finalement dissociées en fragments d'aluminium, de cuivre ou de magnésium avant d'être réemployées en métallurgie.
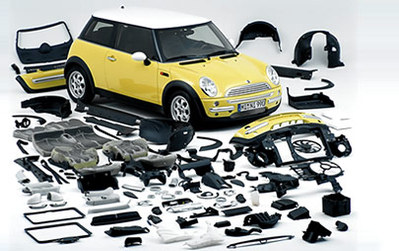
Source : Mini BMW
Déposer un commentaire
Alerte de modération
Alerte de modération